Difficile de faire sans lorsque l’on crée un produit physique. Il faut tester le concept, tester l’assemblage, mais plus encore tester ses fournisseurs !
Revue de prototypage étape par étape.
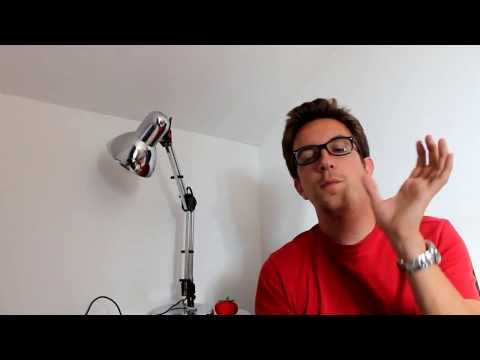
Difficile de faire sans lorsque l’on crée un produit physique. Il faut tester le concept, tester l’assemblage, mais plus encore tester ses fournisseurs !
Revue de prototypage étape par étape.
Peu d’articles sur le blog, ça veut donc dire que… ça bosse dur ! On est en pleine phase de prototypage et c’est une étape cruciale. Si le concept fonctionne, ça voudra dire que je vais avoir beaucoup de travail dans les mois qui viennent : nom, logo, création d’un site internet, industrialisation, e-boutique, blogging et réseaux sociaux, marketing, vente à la sauvette et tout et tout !
Revenons donc un peu sur le prototypage.
Les éléments innovants du produit étant de petite taille, nous avons utilisé des restes de mousse à prototyper (je n’ai pas le nom exact sous la main) pour fabriquer un modèle. Dans notre cas, il aura d’abord fallu créer le modèle dans un logiciel de CAO 3D puis le sauvegarder en IGES (format d’entrée du logiciel qui va créer les trajectoires d’outils). John a ensuite créé les trajectoires d’outils en spécifiant quelles opérations seraient faites pas un foret de gros diamètre puis celles par un foret de petit diamètre et enfin celles par un foret à embout rond pour les finitions. Il a fallu ensuite simuler les trajectoires d’outils dans le logiciel puis sur la machine pour vérifier qu’il n’y a pas d’incohérence et enfin, usiner la pièce. Les pièces font quelques centimètres de côté, mais la durée d’usinage va tout de même de 2 à 5 heures environ. Bien sûr, John est encore en train d’apprendre à se servir des machines et il est probable que l’on puisse aller plus vite en améliorant les trajectoires d’outils et en jouant sur la vitesse de déplacement du foret.
Pour ma part, j’ai récupéré les modèles, les ai retouché (morceau cassé ou ponçage nécessaire) et ai ensuite fabriqué des moules à partir de là. Pour ce faire, on a acheté du silicone, de la cire à parquet et de l’anti adhésif. On applique la cire pour créer une couche protectrice autour du modele en mousse (poreux donc potentiellement absorbant pour le silicone), puis on applique de l’anti adhésif pour éviter que le silicone ne colle au modèle. Enfin, on mélange deux trucs visqueux qui composent le silicone et on coule le tout très délicatement autour du modèle. 16 heures plus tard, le moule est sec et prêt à être démoulé. Il ne reste alors plus qu’à refaire du silicone et à le couler dans le moule après avoir remis une couche d’anti adhésif pour avoir le produit final (ça sèche à côté de moi en ce moment même…). On a eu quelques soucis de bulles qui se forment lorsque l’on mélange le silicone et qui créent des petits trous, mais comme c’est un proto, ça n’a pas beaucoup d’importance. Pour le produit final, il faudra tout de même construire une sorte de caisson avec une pompe pour faire le vide dans lequel on mettra le silicone pour se débarrasser des bulles.
Tout ceci n’est probablement pas très intéressant à lire, mais c’est passionnant à faire ! Et voir le produit que l’on a conçu prendre forme devant ses yeux est super excitant. Bon, on fait encore pas mal d’erreurs, mais on apprend beaucoup.
Voici quelques photos de la fabrication :
Pas encore d’indice sur le produit en lui même, à part ces photos… mais si vous trouvez sans être dans la confidence, vous êtes très forts ! J’attends de valider le concept dans les prochains jours. Si ça ne marche tout simplement pas, il n’est pas exclu de partir sur une toute autre idée. En revanche, si le concept fonctionne, vous allez beaucoup en entendre parler (sur ce blog tout du moins !)
photo credit: ralphbijker via photopin cc